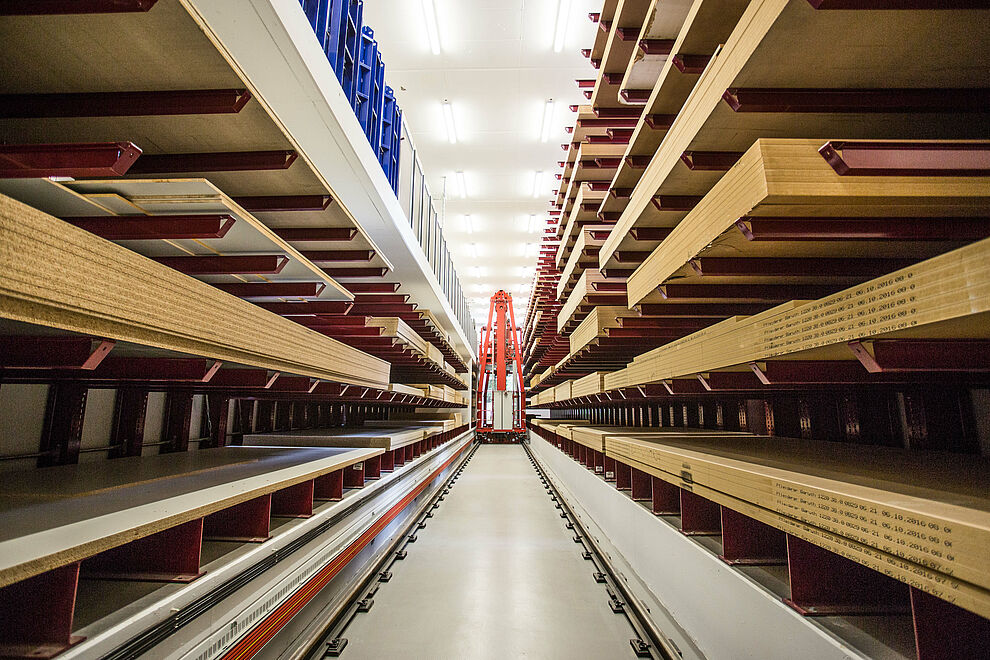
Automatic Storage Systems
Your warehouse needs to work properly to dispatch orders quickly and efficiently. It must be efficient and adapted to requirements: the only way companies stay flexible and competitive on today’s market. Warehouse automation has become such an important competition factor that it is now essential for modern companies.
- Maximum speed + safe handling saves time and money
- Optimal stock overview and perfect order processing on the warehouse management software
- Storage & retrieval machine with cornering technology to access several aisles with a single device
- Retrofitting from semi-automatic to fully-automatic operation at any time
The operating mode of the storage and retrieval machine (SRM) depends on the function of the warehouse. Choose between a semi-automatic or fully automatic warehouse:
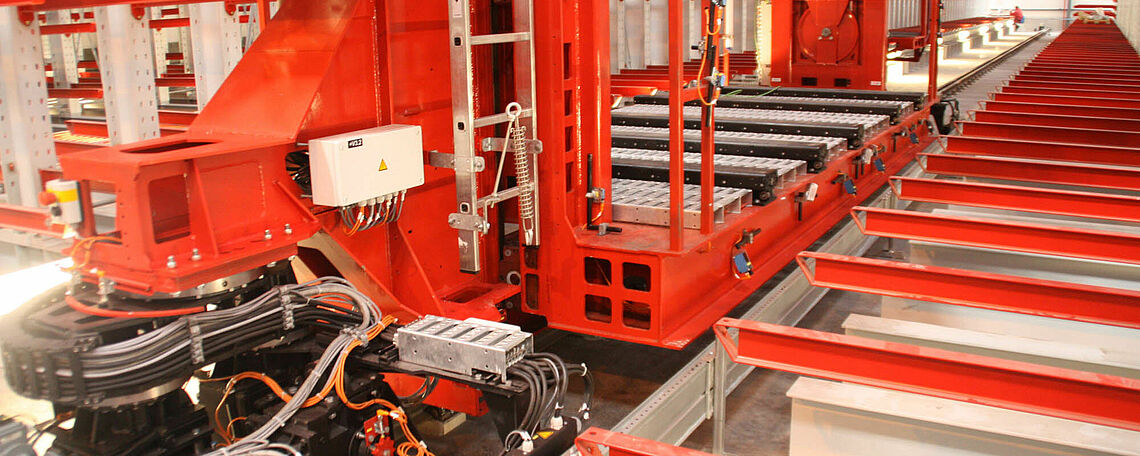
Which racking system is suitable for an automated warehouse?
The basis for an automated warehouse is the suitable automated racking system. The decisive factor for the selection is which products are to be stored and moved. For long goods and bulky goods, cantilever racking is best suited. For palletised goods, the classic pallet rack is the first choice. In principle, almost all racking systems, including shelving for small parts, can be automated. Together with the right conveyor technology and modern software for warehouse management, the automated racking system ensures that the advantages of an automated warehouse are fully exploited: Speed, dynamics, safety, energy and cost savings. The investment in an automated warehouse thus quickly pays for itself.
Automated storage system - your advantages :
- Storage and equipment planning from a single source
- Warehouse management software available
- Wide range of equipment types
- Both curve-going and straight-running units possible
- Up to 8,000 kg load capacity
Semi-automatic warehouse
The semi-automatic warehouse is so named because the warehouse personnel work with the storage and retrieval machine for certain tasks and processes, such as order picking.
The SRM moves automatically to the racking position determined by the operator in advance. The precise positioning in front of the racking position is fully automatic, while the on- and offloading of e.g. wooden boards is controlled by the operator over a manual command. This is also the case for the raising and lowering of loads and for the direction of movement of the forks.
Fully automatic warehouse
In contrast to the semi-automatic warehouse, in the fully automatic warehouse mode, all processes are pre-set on the warehouse management software. All commands are transmitted automatically to the control unit of the storage and retrieval machine. All the steps involved, including start-up of the racking unit, exact positioning in front of the racking position, lifting and lowering of loads, and the journey to the pick-up station are fully automated, without any involvement by warehouse staff.
All the info at a glance:
- Very narrow aisle widths
- Connection to your warehouse management system
- Top storage level up to 20 metres high. Loads of up to 5 tonnes
- One storage and retrieval machine can serve several aisles
- Storage of products up to 8 metres long
Fully automatic order picking warehouse
Storage and retrieval, picking and provision of the order-related packages are fully automated. This not only increases the efficiency of the entire storage and order picking process, but also enables a high area utilisation and reduces damage to the goods. The concept of using the advantages of two-stage picking is completely new: A storage and retrieval machine (SRM) handles the storage and retrieval of packages in the warehouse. If a shipping order requires the picking of different individual sheets, a vacuum manipulator has the corresponding articles ready for shipping, whereby several orders can be processed in parallel. Thus, two separate systems put the orders together very efficiently in the smallest of spaces.
Stacker cranes
A stacker crane is a rail-guided vehicle for handling goods in an automatic racking system. The maximum height of a stacker crane is 46 metres. Depending on the stored goods, weight and dimensions, a distinction is made between different types of stacker cranes. Three of them are described below:
OHRA two-mast stacker crane for long goods and heavy products
With a load-bearing capacity of up to 8 tons, the device from this model range is particularly useful when handling heavy and large-volume goods in high-rise racks is required. This is particularly the case in the building materials, timber, slab or paper-processing industries. Thus, economic storage is possible with a small footprint. Using the “man at the goods” principle, the manual standard devices with standard platforms can be used for direct order-picking at the rack.
OHRA stacker cranes for long goods – your benefits
- Particularly suited for long goods
- Bearing loads of up to 8,000 kg
- Device can be delivered with a platform for manual order-picking
- Curve-operation - handling of several aisles possible
OHRA stacker crane for storage heights of up to 12 m
For automatic storage of Euro pallets and pallet cages in storage heights of up to 12 metres, OHRA provides a special stacker crane model as a true alternative of VNA trucks. The device can be curve-operated, is favourably priced and is based on a modular concept. Its special chassis also allows for direct driving on the hall floor.
OHRA stacker cranes for storage heights of up to 12 m – your benefits
- Particularly suited for order-picking warehouses or automated buffer warehouses
- Building height of up to 12 m
- Alternative for very narrow aisle warehouses
- Curve-operation - handling of several aisles possible
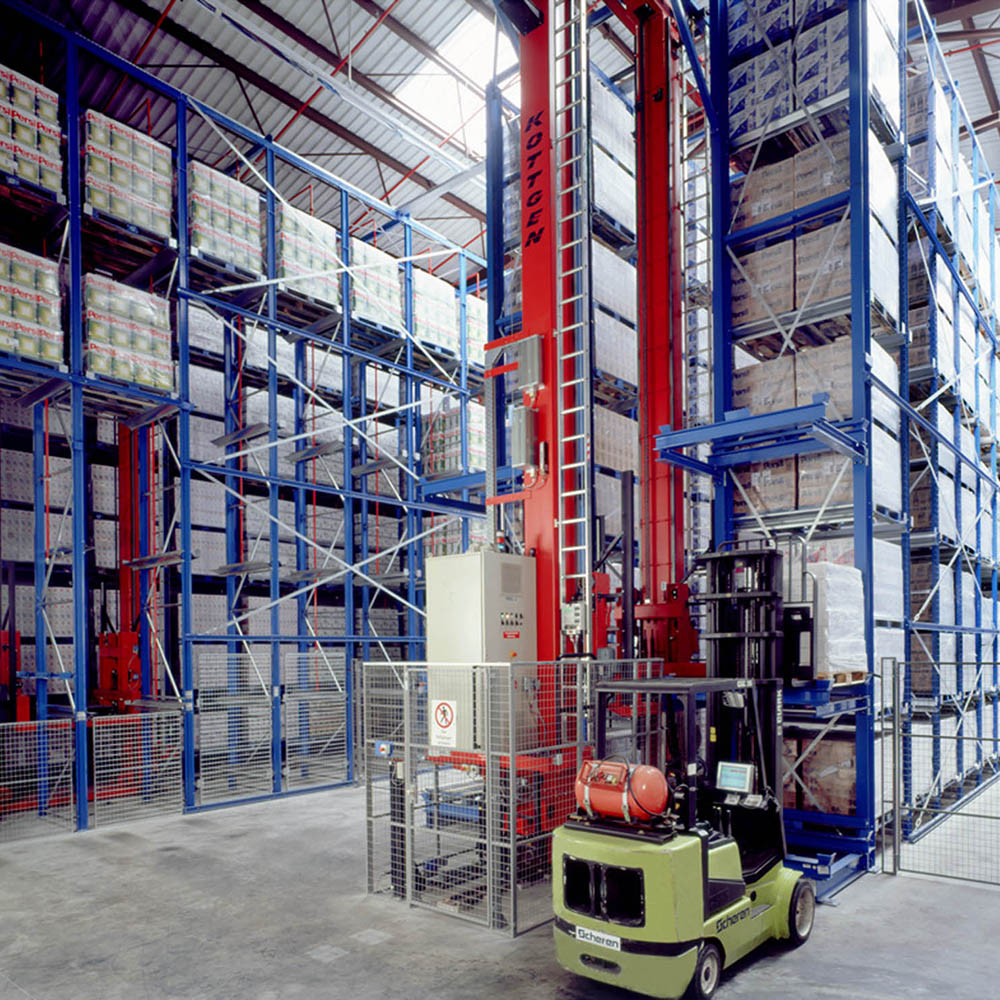
OHRA stacker crane for storage heights of up to 25m
This OHRA stacker crane is intended for storage of pallets and pallet caged materials in high-rise racks of up to 25 metres and has successfully performed in the automation market for decades. Typically equipped with telescopic forks for single- or double-depth storage or alternatively with a shuttle system or special load-carrying device – with customised configuration depending on requirements. Fully automatic option or semi-automatic operation with complete driver’s cabin.
OHRA stacker cranes for high-rise racks – your benefits
- Particularly suited for high-performance warehouses
- For pallets and pallet cages, building heights up to 25 m
- Curve-operation - handling of several aisles possible
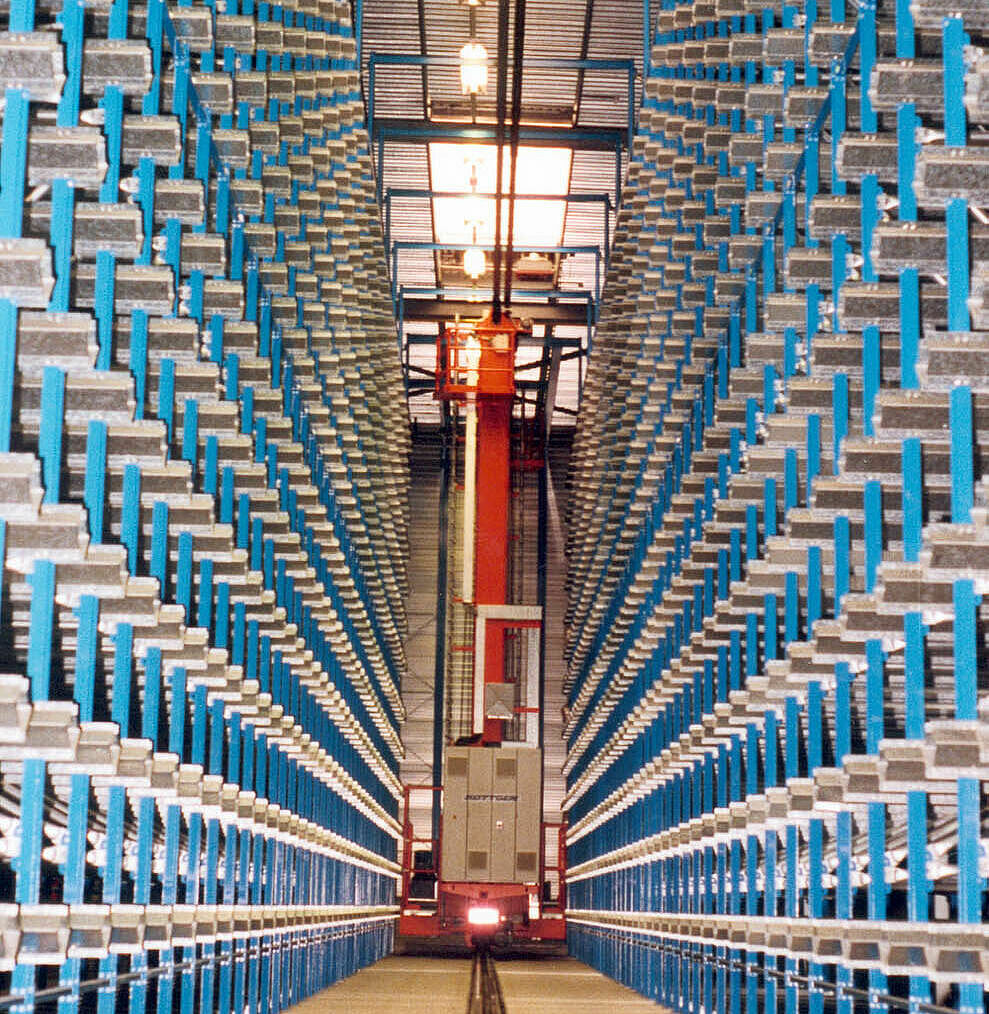
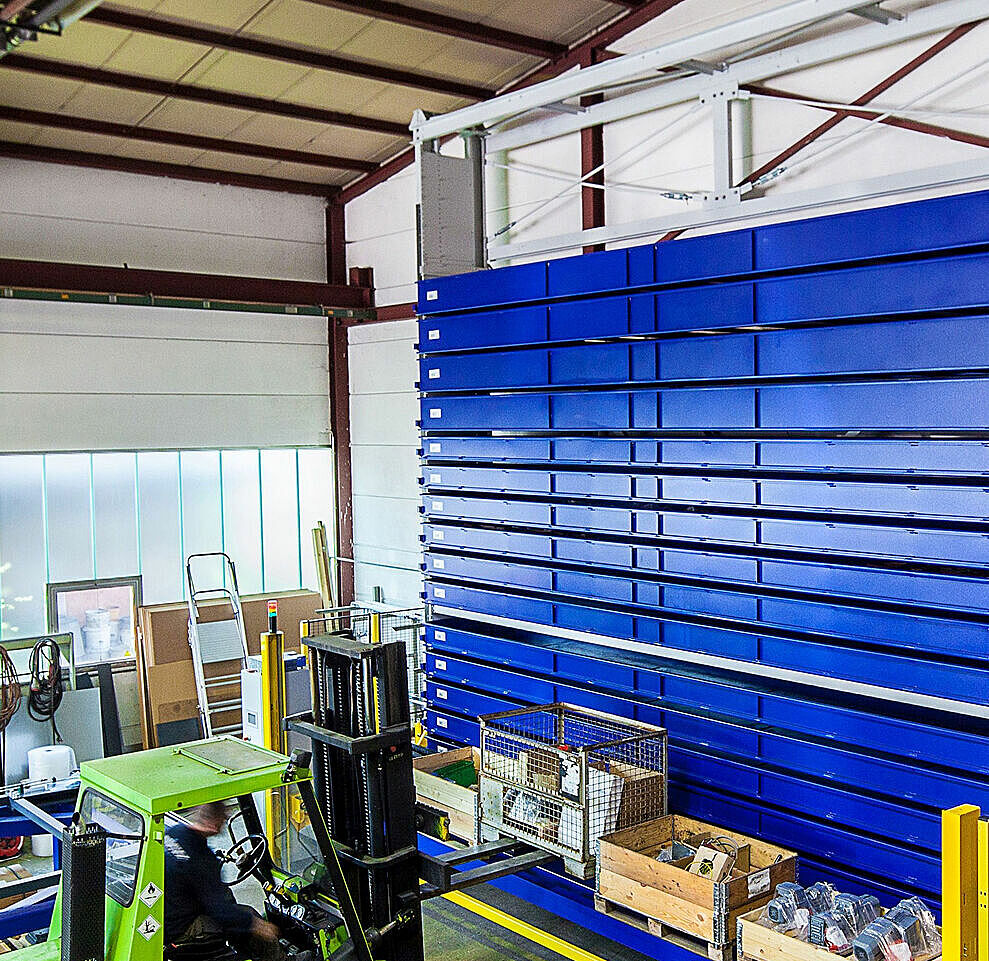
TowerMat
Vertical Lift Storage System for Heavy Loads – Available in Three Versions
The TowerMat is ideal for space-saving storage of long goods, sheet metal, or pallets—especially where warehouse heights should be used efficiently. This vertical storage system is modular and flexibly adapts to both the stored goods and the building’s structural conditions. Depending on the version, cassettes or system pallets with weights of up to 8 tons can be accommodated. Goods are automatically delivered to the operator according to the “goods-to-person” principle.
Three variants are available for different storage requirements:
1. TowerMat TM-EE is suitable for small to medium storage volumes and offers a compact solution for limited floor space.
2. TowerMat TM-FE is designed for medium storage capacities and, thanks to multiple storage towers and a central stacker crane, enables particularly high efficiency.
3. TowerMat TM-RE is the most powerful version, designed for large storage volumes, featuring a side-traveling stacker crane along several storage towers.
System Features:
- Flexible design for storing long goods, sheet metal, or pallets
- Load capacity up to 8 t per storage location, total payload up to 400 t
- Machine heights up to 25 m possible
- Efficient storage and retrieval via integrated stacker crane
- Single-row or multi-row configurations available
- Optional rear operation or roof penetration
The TowerMat system can be easily integrated into existing logistics processes and increases storage capacity even in the smallest spaces.
PickMat – Automated Handling System for Laser Processing
The PickMat automates material supply for laser machines and ensures smooth processes in sheet metal processing. The system handles both the feeding of raw material and the return storage of cut sheet metal parts. Reuse of leftover sheets is easily possible. Reduced loading and unloading times lead to a significant increase in productivity throughout the manufacturing process.
Key Advantages:
- Automated connection to laser cutting systems
- Integration into existing storage systems possible
- Compatible with common manufacturers
- Short loading and unloading cycles
- Gentle and safe material handling
- Customer-specific layout
PickMat is particularly suitable for companies that want to combine high utilization in sheet metal production with automated storage technology.
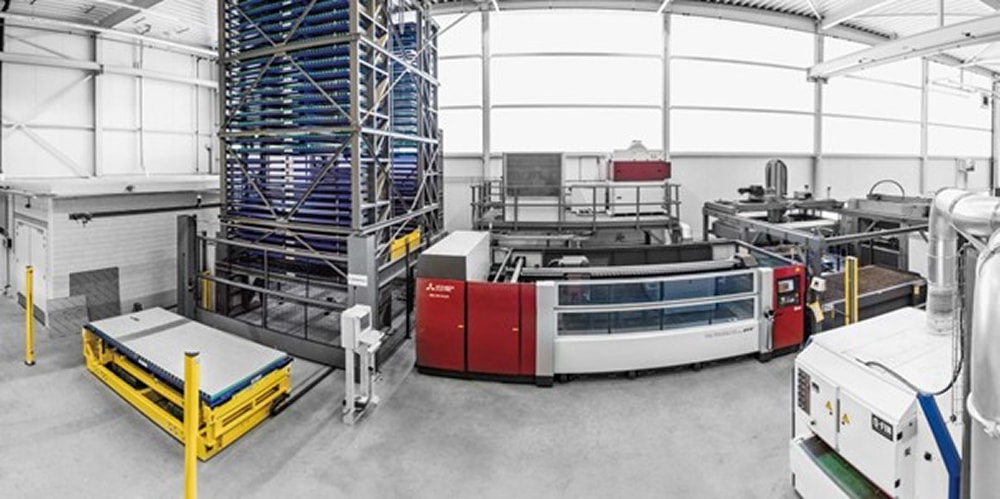
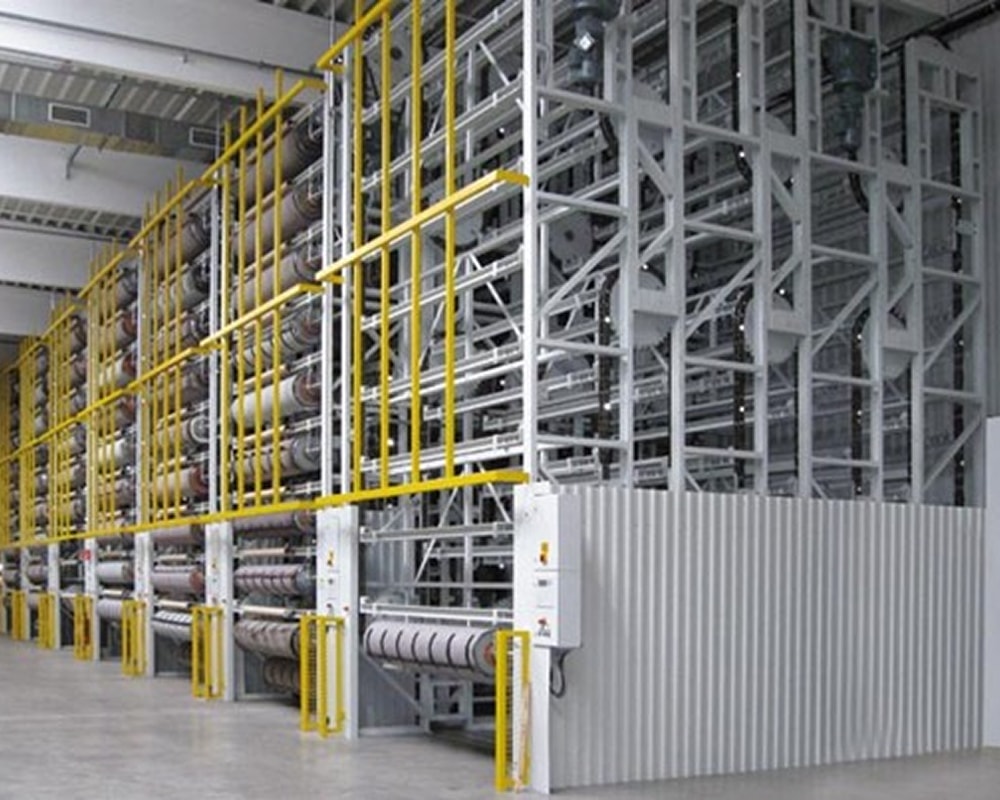
InterMat – Carousel Storage System Based on the Paternoster Principle
The InterMat system is an automated carousel storage system operating on the paternoster principle. Stored goods are delivered to the operator at the push of a button—quickly, reliably, and without manual searching. Typical applications include storage of long goods, cable drums, cylinders, or rolled materials.
Technical Highlights:
- Carousel principle with access-optimized carrier control
- Especially suitable for long goods, tires, rolls, or tools
- Vertical and horizontal space utilization possible
- Special sizes and customer-specific designs available
- Ideal for pits, bridge constructions, or tight spaces
Thanks to its flexible design, the InterMat can be optimally integrated into existing production or logistics areas and makes effective use of unused overhead space.
Warehouse management software
The entire material flow of a warehouse or a production facility can be controlled fully automatically. Our strengths are especially in scenarios with new products, where the goal is to adjust the logistics system to your existing organisation structure, not the other way around(!). The basis for this is an initial analysis of the actual situation and a jointly deduced future forecast. Based on the data collected on item turnover and company structure, we will develop solution concepts together with your employees. These will later be used as a specification book for automated storage.
OHRA warehouse management software - digital automation
The WMS is a comprehensive and optionally configurable standard system. You can achieve fast and lasting cost savings through optimum deployment of employees and technical system and simultaneous improvement of the process quality and reduction of the storage volume.
OHRA warehouse management software
- Analysis of the actual situation
- Solution development
- Presentation of results
- Compilation of the specifications book
- Optimisation of storage capacity
- Fifo-Lifo-BBD
- ABC classification
- Blocking of bays/stock
- Order-picking optimisation
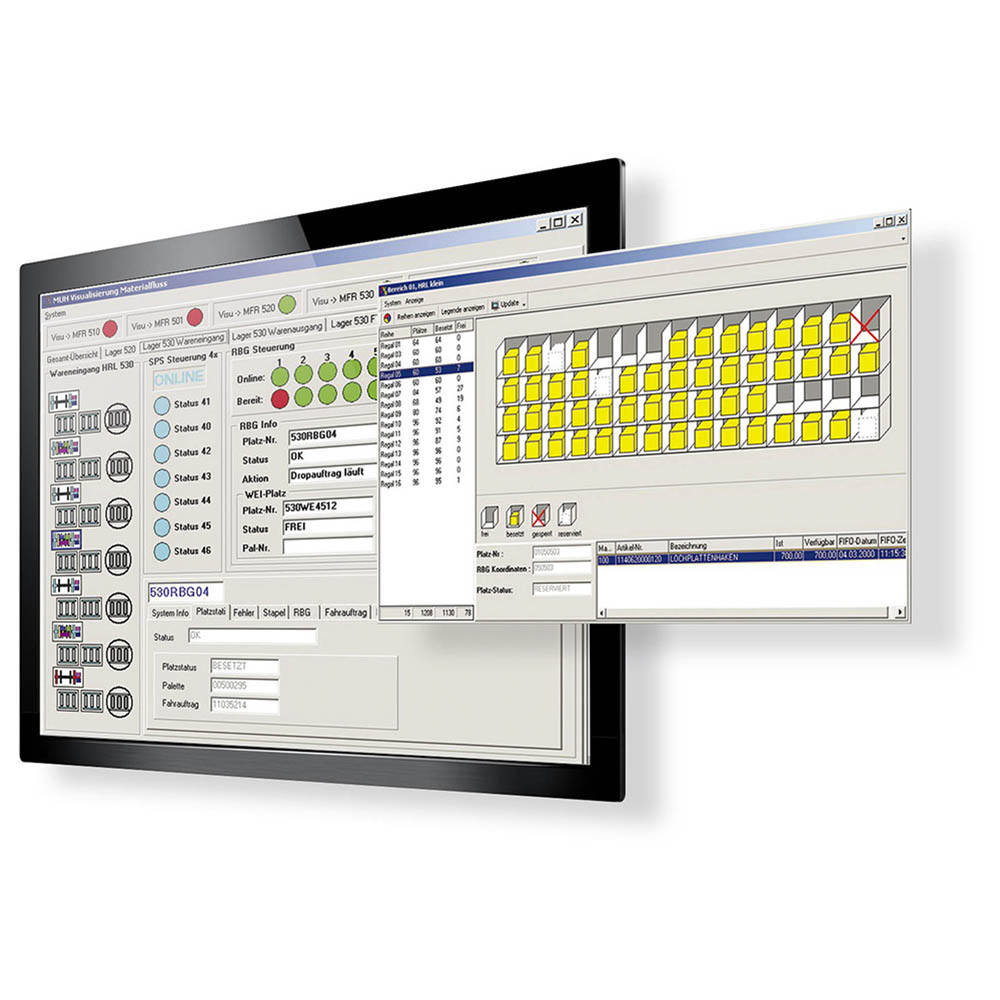